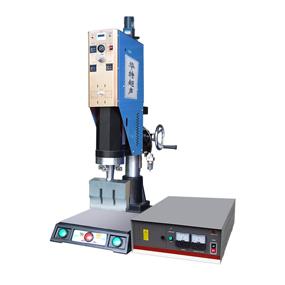
Ultrasonic welding mold
Ultrasonic welding moldThe design includes ultrasonic mold amplitude, ultrasonic mold frequency parameters, ultrasonic mold processing accuracy, ultrasonic mold service life, etc., and learn welding knowledge together. 1. Amplitude is a key parameter of welding materials, which is equivalent to the temperature of ferrochrome. If the temperature cannot be reached, no welding is performed. Too high temperature will scorch the raw materials or damage the structure, resulting in poor strength. Because each company chooses a different sensor, the output amplitude of the sensor is different. After using different ratio horns and welding heads, the working amplitude of the welding head can be corrected to meet the requirements. Under normal circumstances, the output amplitude of the transducer is 10-20μm, and the working amplitude is generally about 30μm. The transformation ratio of the horn and the welding head is the same as the shape of the horn and the welding head. When the front-to-back area ratio is an exponential, function, and other shape stepping, the front-to-back area ratio is proportional to the total transformation ratio. Your company chooses welding machines of different brands. The simple method is to make according to the size of the working welding head to ensure the stability of the amplitude parameters. 2. Frequency parameters of ultrasonic molds Any company's ultrasonic welding machine has a center frequency, such as 20kHz, 40KHz, etc. The working frequency of the welding machine is mainly determined by the mechanical resonance frequency of the transducer, booster and horn. Adjust the generator frequency according to the mechanical resonance frequency to achieve consistency and make the welding head work in resonance. Each part is designed with a half-wavelength resonator. The resonant frequency of generator and machinery has a resonant working range. Generally, when the setting is ±0.5KHz, the welding machine can basically work normally within this range. When we make each welding head, we will adjust the resonance frequency. The error between the resonant frequency and the design frequency is required to be less than 0.1khz. For example, for a 20kHz welding head, the frequency of our welding head is controlled at 19.90-20.10khz, with an error of 5‰.